1.In-Place Material Reuse: Cold recycling machines grind the existing pavement layers, including the asphalt and sometimes parts of the subgrade, to create a uniform mix. This approach minimizes the need for new materials and allows for direct reuse of existing pavement, which helps stabilize the subgrade while saving costs and resources.
2.Enhanced Structural Integrity: By blending in binding agents like cement, lime, or bitumen, cold recycling machines help stabilize the subgrade, improving its strength and durability. This leads to a subgrade that can handle higher loads and withstand environmental stress, increasing the overall lifespan of the roadway.
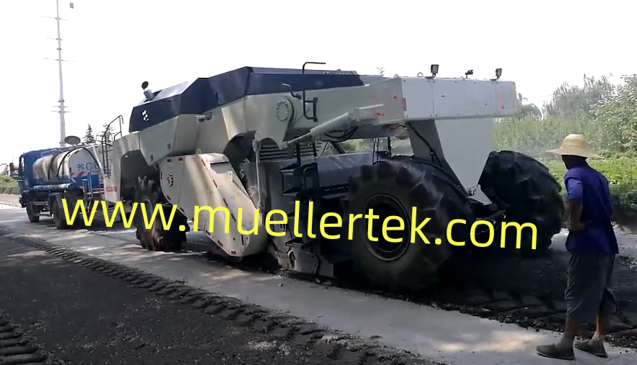
3.Environmentally Friendly Process: Cold recycling significantly reduces the need for hauling away old materials and bringing in new aggregates, leading to lower emissions and fuel consumption. This eco-friendly method is especially valuable in road rehabilitation projects, where sustainability is a priority.
4.Efficient and Cost-Effective: Using a cold recycler is generally faster than full-depth reconstruction, reducing project time and minimizing traffic disruption. It’s also more economical, as it cuts down on material and transport costs, making it an ideal solution for large-scale highway repairs.
5.Improved Pavement Quality: The process results in a strong, stable, and moisture-resistant base layer, which is key to a durable pavement structure. This optimized subgrade quality is crucial for preventing issues like cracking, rutting, and potholes, ultimately leading to a safer and smoother road surface.
Overall, cold recyclers are instrumental in restoring subgrade quality and ensuring highways remain strong, safe, and long-lasting.